1 引言
當前,一些學者對厭氧反應器流場和水力學性能進行了研究,例如,應用湍流模型模擬了側(cè)伸攪拌式厭氧反應器流場,季軍遠等(2012)采取多釜串聯(lián)及擴散模型模擬了分段組合式厭氧反應器行為,通過測定停留時間分布研究了厭氧反應器中不同反應區(qū)的流動特征.這些研究取得了一定成果,但由于模型相對簡單,對于構(gòu)造復雜的內(nèi)循環(huán)厭氧反應器不能完全適用.同時,將動力學方程和流動模型結(jié)合以模擬厭氧反應器中反應過程的研究則較少有文獻涉及.基于此,本文在建立厭氧反應動力學方程后,針對自主設計的內(nèi)循環(huán)厭氧反應器采取組合模型進行模擬研究.厭氧反應過程中由于有氣體生成,氣體從產(chǎn)生到形成氣泡,以及氣泡在反應器中的向上運動必然會對整個反應器的流動型式產(chǎn)生重大的影響,使得反應器的流型偏離于理想狀況.為此,本文通過測定實際反應器中流體的停留時間分布,根據(jù)停留時間分布的特征提出流動的組合模型,并據(jù)此研究實際的反應過程,以期為內(nèi)循環(huán)厭氧反應器的進一步工業(yè)化放大提供有益的開發(fā)思路和方法.
2 實驗方法
接種污泥為某啤酒廠UASB反應器中活性污泥 ;營養(yǎng)液參照產(chǎn)甲烷活性測定營養(yǎng)液配制方法進行配制;牲畜廢水為牲畜糞便經(jīng)過淘洗、過濾去除大顆粒泥沙及部分懸浮物后所得的液體,糞便取自某養(yǎng)豬場;示蹤劑為硝酸鈉(分析純),由杭州化學試劑有限公司提供.
主要儀器:FA1104N型電子天平、DFG-9053A型電熱恒溫鼓風干燥箱、TC-15型恒溫電熱套、SC-15型數(shù)控超級恒溫槽、BT01-YZ1515型蠕動泵、GC-1690B型氣相色譜儀
2.1 內(nèi)循環(huán)厭氧反應器主反應區(qū)停留時間分布密度函數(shù)E(t)的實驗測定流程
為建立厭氧反應器的流動模型,實驗研究了反應器停留時間分布,并考察了不同氣體流量的影響,獲得了停留時間分布函數(shù).內(nèi)循環(huán)厭氧反應器由主、次兩反應區(qū)組成,由于反應主要在主反應區(qū)4進行,因此,實驗主要針對反應區(qū)4進行停留時間分布測定.實驗流程如圖 1所示.
圖1 工藝流程示意圖(1.進水罐,2.蠕動泵,3.氣泵,4.主反應區(qū),5.內(nèi)反應區(qū),6.出水口,7.氣體出口,8.反應液出口,9.環(huán)隙反應區(qū))
以水為工作介質(zhì),將水加入進水罐至一定高度,開啟蠕動泵,保持水流量為15 L · h-1,流量計安裝在泵出口處;同時開啟氣泵,氣泵流量由安裝在泵出口處的氣體流量計檢測,分別為0、90、180 mL · h-1.水從下而上流過反應器,反應器分為上下兩部分,下部為主反應區(qū),內(nèi)徑為110 mm,高550 mm,幾何體積為5 L;上部為次反應區(qū),又分為兩部分,一是內(nèi)反應區(qū)5,另一為環(huán)隙反應區(qū)9,環(huán)隙反應區(qū)幾何體積VR4為2.44 L,內(nèi)反應區(qū)幾何體積VR5為2.86 L.在環(huán)隙反應區(qū)的上部安裝有氣體出口管,由于測定的是主反應區(qū)停留時間分布,故液體在主反應區(qū)上部出水口處排出,出水口處同時安裝一電導儀,通過檢測出口液體的電導率而推算出示蹤物濃度的高低.
當氣液兩相流動達到穩(wěn)定后,在進水罐上方快速加入一定量的示蹤劑,同時計時,間隔一定時間,于反應器出口處記錄下水的電導率隨時間的變化.
2.2 驗證實驗工藝流程
驗證實驗工藝流程示意圖如圖 2所示.新鮮料液加入儲槽中,料液由蠕動泵輸送,進入換熱器中,換熱器由10根有機玻璃管組成,管外徑為10 mm,長65 mm,料液走管程,與循環(huán)水換熱后進入反應器,在次反應區(qū)頂部進行氣液分離,液體進入廢液槽,氣體經(jīng)過氣體流量計后由緩沖瓶進入液封槽,液封槽容積為1500 mL,最后進入皂沫流量計計量放空.
圖2 驗證實驗工藝流程示意圖(1.原料液儲槽,2.蠕動泵,3.流量計,4.換熱器,5.反應器,6.反應廢液槽,7.氣體流量計,8.液封槽,9.緩沖瓶,10.皂沫流量計)
由于新鮮料液配料較為困難,當系統(tǒng)穩(wěn)定,即氣體流量變化不大時,每隔4 h分別測量氣液兩相組成、流量,一般測量2~3次結(jié)束實驗.
2.3 內(nèi)循環(huán)厭氧反應器主反應區(qū)流動模型建立
對反應器主反應區(qū)流動狀況作出如下假設:示蹤物A為瞬間脈沖進料;反應器中氣體流量恒定不變,且均勻上升;進料清水流量亦恒定不變.現(xiàn)假設厭氧反應器主反應區(qū)流動型態(tài)可由一平推流區(qū)(PFR)與兩個并聯(lián)的全混區(qū)(CSTR)串聯(lián)組合而成,模型示意圖如圖 3所示.
圖3 中反應器流動模型組合示意圖文名
設反應器主反應區(qū)總體積為VR,等于模型中各反應區(qū)體積VRi之和,設PFR的體積分率為f1,CSTR2、CSTR3的體積分率分別為f2、f3,總流量為v0,流經(jīng)CSTR2的流量分率為I,某時刻流出CSTR2、CSTR3全混區(qū)的流體中示蹤劑濃度分別為CA2、CA3,混合后出口總濃度為CA.當t=0時,在PFR反應器入口處,脈沖法加入質(zhì)量為M的飽和示蹤劑A.對于PFR:
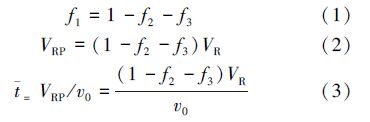
式中,VRP為PFR的體積(L); p為流體在PFR中的平均停留時間(min).
對CSTR2進行物料衡算,求取CSTR2出口濃度CA2:①當t< p時,由于示蹤劑A仍在PFR中,對CSTR2,CA2=0;②當t≥t¯t¯p時,對CSTR2作物料衡算,根據(jù)輸入量=輸出量+累計量,則有:
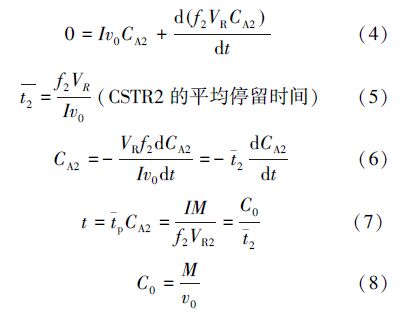
求解該方程,得

同理,對CSTR3進行物料衡算,可求取CSTR3出口濃度CA3:①當t< t¯t¯p時,由于CSTR3中無示蹤劑,故CA3=0;②當t≥ t¯t¯p時,對CSTR3作物料衡算,可得:
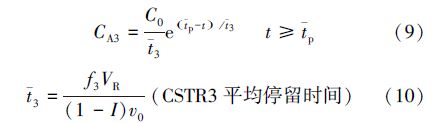
最后,對CSTR2、CSTR3出口處作物料衡算,由于該處進行的是混合過程,則:①當t< t¯t¯p時,CA=0;②當t≥t¯t¯p時,CA=ICA2+(1-I)CA3.
停留時間分布密度函數(shù)E(t)的求取公式如下:
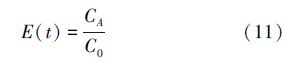
當t . 最后:
對模型求解轉(zhuǎn)化為求解一個三參數(shù)I、f1、f2的E(t)方程,其中,t¯t¯p不是獨立的. 3 實驗結(jié)果及模型參數(shù)求解 3.1 主反應區(qū)停留時間分布測定 實驗是在清水流量為15 L · h-1,氣體平均流量分別為0、90.0、182.1 mL · h-1條件下進行測定的,示蹤劑脈沖加入,部分實驗數(shù)據(jù)如表 1所示. 根據(jù)
,各時間點的E(t)值如表 2所示.應用非線性最小二乘法求解,不同氣體流量時的模型參數(shù)及方程如表 3所示. 表2 停留時間分布密度函數(shù)E(t)隨時間變化關系 當vg=0、90.0、182.1 mL · h-1時,分別獲得E(t)方程.E(t)方程獲得后,將不同時刻t時的CA值,代入方程,可獲得E(t)的計算值,其值列于表 2中.由表 3中數(shù)據(jù)可知,隨著氣體流量的增大,反應器中存在較大的返混,PFR體積所占比率f1不斷減小,說明氣體流量對反應器的流型有著較大的影響.
3.2 內(nèi)循環(huán)厭氧反應器模擬 3.2.1 內(nèi)循環(huán)厭氧反應器反應過程模型的建立及驗證 1)反應器反應過程模型建立 根據(jù)以上停留時間分布的特點,厭氧反應器由主、次反應區(qū)組成,因此,可用圖 4中的組合模型模擬反應器反應過程行為.圖 4所示組合模型中,根據(jù)停留時間分布規(guī)律,1、2、3擬合的是厭氧反應器主反應區(qū);次反應區(qū)由中間回流區(qū)和環(huán)隙區(qū)構(gòu)成,中間回流區(qū)可作為平推流處理,環(huán)隙區(qū)由于有大量產(chǎn)物氣體流過,可作為全混區(qū)處理,所以反應器次反應區(qū)可由4、5并聯(lián)進行擬合. 圖4 反應器反應過程模型組合示意圖 模型中各參數(shù)的確定:針對本反應器,實際反應過程中生成的氣量在90~180 mL · h-1之間,因此,模型中主反應區(qū)各參數(shù)取其平均值,具體如下:f1=0.36,f2=0.53,f3=0.11,I1=0.53. 次反應區(qū)流量分率為:
各反應區(qū)有效體積VRi的確定:總污泥加入量為5 L,上層即次反應區(qū)污泥所占分率按0.35計算,則:VR1+ VR2+VR3=3.25L,VR1=1.17L,VR2=1.7225L,VR3=0.3575L,VR4+ VR5=1.75L,VR4=V4/(V4+ V5)=0.8057L,VR5=0.9443L. 2)模型驗證 為驗證上述模型是否正確,進行了3組不同初始濃度操作狀態(tài)的實驗,當厭氧反應器操作穩(wěn)定后,即在一定時間能氣體流量基本不變,此時,操作參數(shù)分別為:廢液體積流量v0L=15 L · h-1,溫度T=35 ℃,廢液初始COD CS0=3.3840、3.5326、3.8729 g · L-1,由前期實驗所得動力學方程為:
式中,Cs為反應器中廢液濃度(g · L-1),-rs為廢液COD消耗速率(g · min-1 · L-1),rpCH4為甲烷生成速率(g · min-1 · L-1),rpCO2為二氧化碳生成速率(g · min-1 · L-1),模擬計算了反應器單程轉(zhuǎn)化過程,主、次反應區(qū)出口即B、C兩點處計算值如表 4所示.以基質(zhì)初始濃度CS0=3.3840 g · L-1為例,實驗數(shù)據(jù)及處理如表 5所示. 表4 主、次反應區(qū)出口處B、C兩點狀態(tài)數(shù)據(jù) 表5 驗證實驗各點狀態(tài)數(shù)據(jù)一覽 CH4體積流量vCH4實為193.81 mL · h-1,CH4質(zhì)量流量FCH4實為2.045×10-3 g · min-1.同理,可計算CO2體積流量、質(zhì)量流量分別為8.75 mL · h-1、2.54×10-4 g · min-1.誤差按(實驗值-計算值)/實驗值×100%計算,可知本組B點基質(zhì)濃度CSB誤差最大,為7.86%. 由表中數(shù)據(jù)可見:不同時刻反應器出口C點的氣體體積流量v大于模擬計算時的體積流量vgC,其原因可能是該驗證實驗時間不夠長,系統(tǒng)中存在一定的N2,同時反應過程中生成其它氣體所致.其余兩組數(shù)據(jù)計算依此類推,最后得到不同濃度時,C點出口處CH4體積流量最大誤差為9.67%,CO2體積流量最大誤差為8.53%,可見所建立的組合模型能夠反映反應器實際操作狀況. 3.2.2 內(nèi)循環(huán)厭氧反應器模擬計算 根據(jù)以上反應過程模型,模擬了初始COD、溫度變化對厭氧反應器狀態(tài)的影響. 1)初始COD變化對反應器操作狀態(tài)影響的模擬研究 操作參數(shù)為:廢液體積流量v0L=15 L · h-1,溫度35 ℃,改變COD初始值,B、C兩處模擬數(shù)據(jù)如表 6所示.由表 6中數(shù)據(jù)可知,當溫度一定時,隨著基質(zhì)初始濃度的增高,B、C兩處基質(zhì)濃度也隨之升高,產(chǎn)物CH4、CO2的質(zhì)量流量也升高. 表6 反應器出口處B、C兩點狀態(tài)隨基質(zhì)濃度變化關系 2)反應溫度變化對反應器操作狀態(tài)影響模擬研究 操作參數(shù)為:廢液體積流量v0L=15 L · h-1,COD初始值CS0=3.40 g · L-1,改變溫度,B、C兩處模擬數(shù)據(jù)如表 7所示.由表 7中數(shù)據(jù)可知,在基質(zhì)初始濃度一定時,隨著溫度的升高,B、C兩處的基質(zhì)濃度不變,這主要是由于在該溫度范圍內(nèi),基質(zhì)消耗活化能很低,以致消耗速率幾乎不隨溫度變化而形成的結(jié)果;但產(chǎn)物CH4、CO2的質(zhì)量流量隨溫度的升高而升高,同時CO2的增加速率要快于CH4,這主要是由于CO2生成活化能高于CH4,故其生成速率對溫度更為敏感.具體參見污水寶商城資料或http://www.yiban123.com更多相關技術文檔。 表7 反應器出口處B、C兩點狀態(tài)隨基質(zhì)溫度變化關系 4 結(jié)論 1)通過對反應器主反應區(qū)停留時間分布的考察,主反應區(qū)流型可以用一平推流區(qū)與兩個并聯(lián)的全混區(qū)進行串聯(lián)組成,各區(qū)所占體積分率隨反應過程中所產(chǎn)氣體流量不同而不同,隨著氣體流量的增大,平推流區(qū)所占體積分率減小. 2)次反應區(qū)由平推流區(qū)和全混區(qū)并聯(lián)組合而成,整個厭氧反應器由主反應區(qū)和次反應區(qū)串聯(lián)組合而成,根據(jù)實驗數(shù)據(jù)可知,C點出口處CH4體積流量最大誤差為9.67%,在可允許的范圍內(nèi),說明該組合模型較好地模擬了反應器的實際狀態(tài). 3)采取單因素分析方法,模擬了基質(zhì)初始COD和溫度變化對反應器出口狀態(tài)的影響,發(fā)現(xiàn)產(chǎn)物CH4、CO2的質(zhì)量流量隨基質(zhì)濃度、溫度的升高而升高;在304.15~312.15 K范圍內(nèi),溫度的變化對出口處基質(zhì)濃度的影響不大.
表1 不同氣體流量時分布電導率隨時間變化關系
表3 不同氣體流量時流動模型參數(shù)計算值